I started building things from wood in the Summer of 2020, when I was unemployed, and after one of my roommates vacated his bedroom. I had been attracted to the idea for a long time, and was watching a lot of videos from Matthias Wandel, whose general approach I admired. I was particularly enchanted by his wooden pipe organ.
A lot of decent wood is discarded in my neighborhood, within walking distance of my apartment. From the start, I've tried to build things entirely or almost entirely from these discarded scraps. The quality of material varies, but for my purposes (and at my very rudimentary skill level) the garbage usually does the job. I didn't have any tools to start with, so bought an old Skilsaw on craigslist and got to work.
My workshop
Though my first projects were done in the temporarily-vacant room in my apartment, I quickly found that sawing wood indoors is a terrible idea, for reasons that should be obvious (but which I chose to ignore).
Fortunately, my apartment sits above a laundromat whose northern wall has no windows, with a very wide adjacent sidewalk.
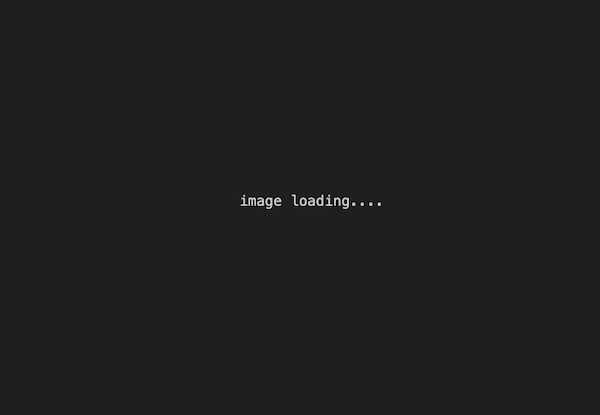
I've found I can run an extension cord out of my window and set up on the sidewalk without, as far as I can tell, bothering anyone.
I can't leave anything on the street, so when I start working this way I typically plan to be out there for a while. Occasionally, people will approach me and talk to me. I had been self-conscious about displaying my unskilled and occasionally clumsy carpentry to the public, but I've gotten used to the exposure and enjoy the spontaneous conversations with neighbors.
Projects
(listed here in chronological order)
Silverware organizer
This was the second project I made, after a three-legged folding workbench that has not survived. The material was a small piece of thin fiberboard that I found on the sidewalk. I wish I had a picture of it, to demonstrate just how shitty it was; part had gotten wet and was a little soggy.
Partly because I wanted to fully seal up the originl material, this is the only project that I painted. I used acrylic paint and a polyurethane topcoat.
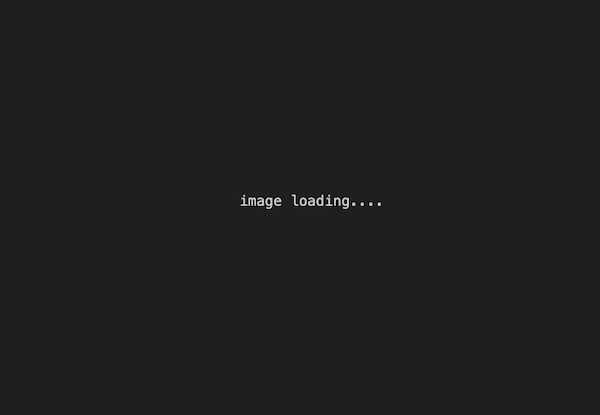
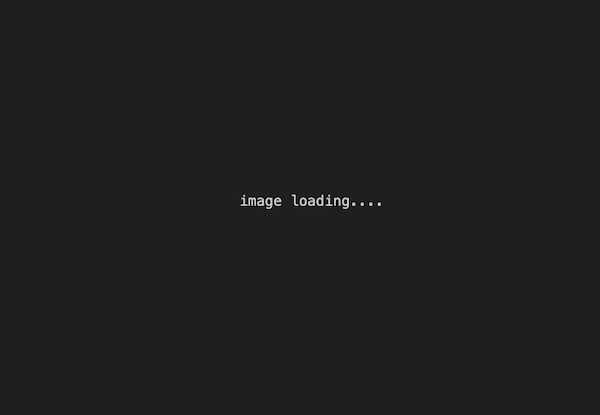
Misc/shoe rack
I was very lucky to find two sheets of nice, 1/4" maple plywood on the sidewalk in Park Slope, from which I made two projects and have a third in progress. This was the first.
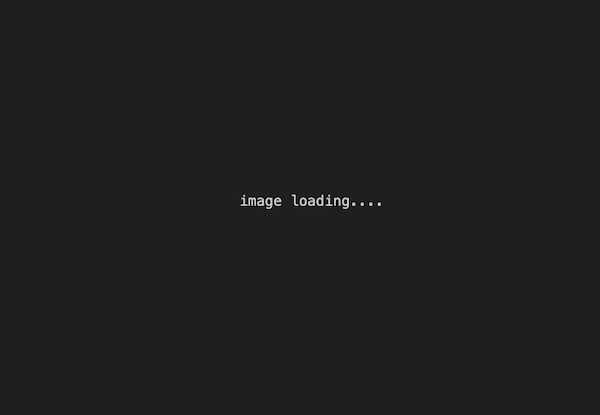
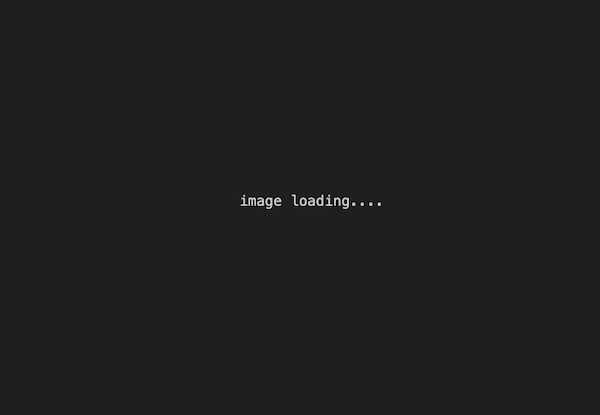
Each edge frame was joined together with dowels (the two cross beams) and rabbets (the top beam). The two racks sit on top of those cross beams, glued directly without any special joinery.
Large utensil holder
Made from the same maple plywood as the shoe/misc rack, this was as much an effort to address a practical organizational need as it was an attempt to achieve a certain puzzle-box aesthetic, which is amplified by the visible layers of the plywood.
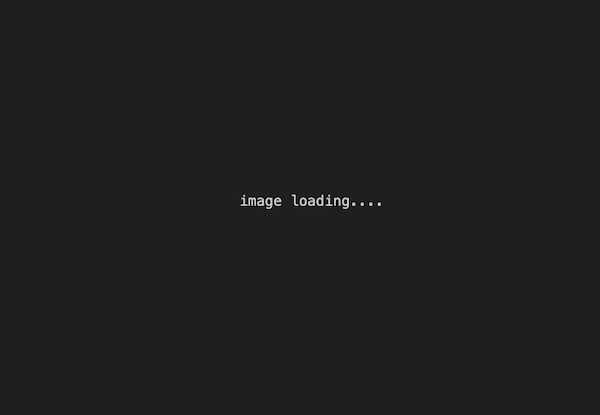
The rabbet joints proved to be quite difficult to close given my imprecise cuts. Fitting the whole thing together and gluing it up really did feel like a puzzle, and a stressful one; I'm surprised that it held together as well as it did.
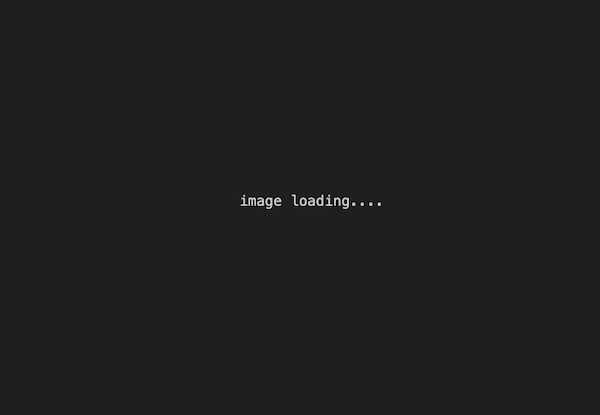
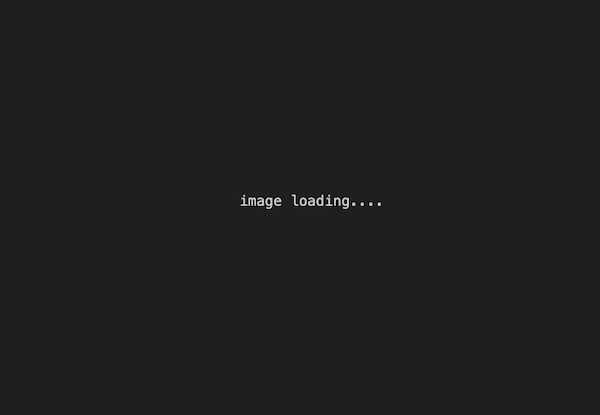
Kitchen table
I had been wanting a table in our kitchen for a long time, but given the limited space available, it was difficult to find a right-sized table or justify a purchase. Building one myself out of discarded materials meant I could determine the dimensions myself and spend nothing (except the cost of glue).
The material usage, born out of necessity/availability, is the inverse of what it should be: a softwood tabletop and hardwood apron/legs. The hardwood all comes from a butcher block that was conveniently left out by people moving out of our building right in my woodshop:
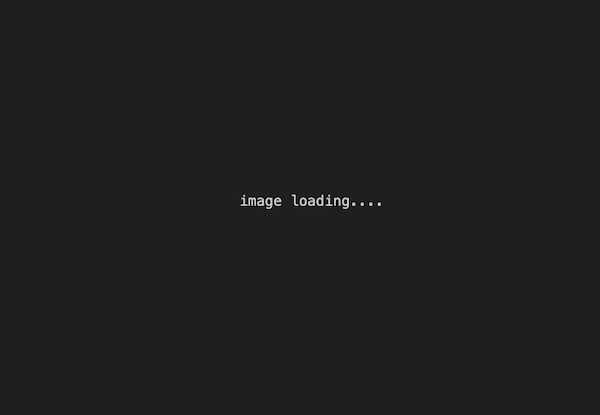
I built the frame in what I think is a typical way, joining the apron rails together at the corners with diagnoal braces and affixing the legs to the apron rails with dowel joints.
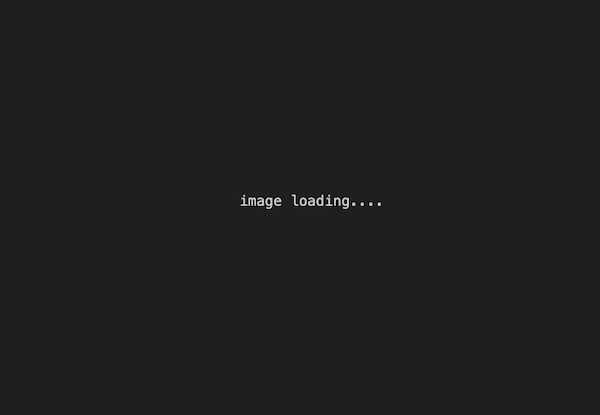
The tabletop is made from douglas fir planks that I got on the facebook "Buy Nothing" group. I edge-joined the planks to form the tabletop, and reinforced the joints with dowels.
It isn't advisable to edge join boards whose edges aren't perfectly square. If I had a more sophisticated workshop with a table saw or jointer, it might have been easier for me to square up the edges before joining the boards. I do regret not attempting something like that with my circular saw, but I'm not sure if the results would have been much better.
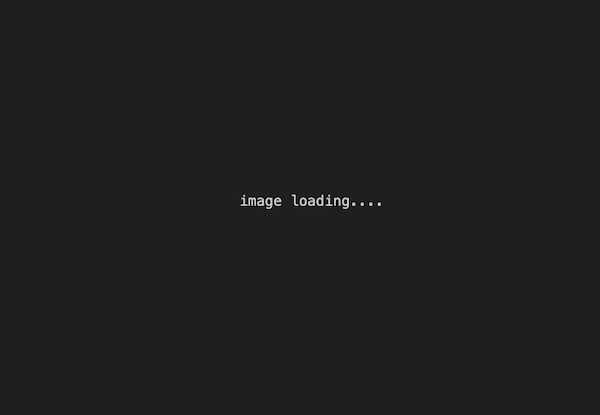
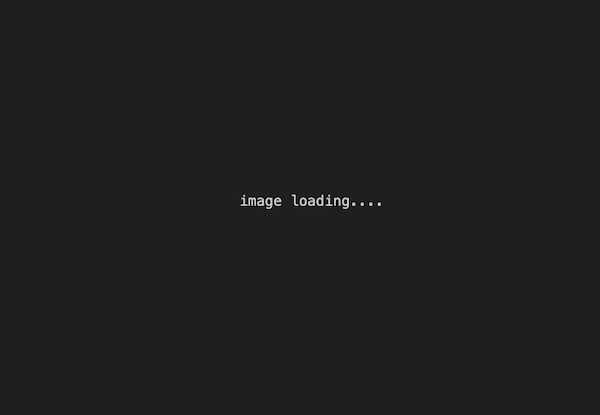
In spite of my best efforts, the tabletop came out a bit warped, and pulls two of the legs slightly off the floor as a result. Fortunately, putting some thin plywood or coasters under each of the lifted legs makes the problem almost unnoticable.
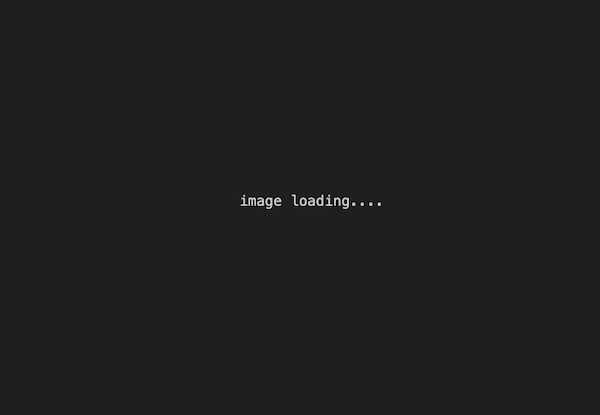
Bread box
I originally wanted to build a plain wood box to keep our toaster in, because mice had invaded our kitchen and were attracted to the toaster. It proved more practical to just keep the toaster elsewhere, and use the box for bread products.
Because it's just a simple box, this project presented no major challenges and came out without any big screwups. In that senses it's unique among my wood projects.
The only materials are glue and softwood boards that were originally sold by Ikea as shelves. A neighbor discarded three of them.
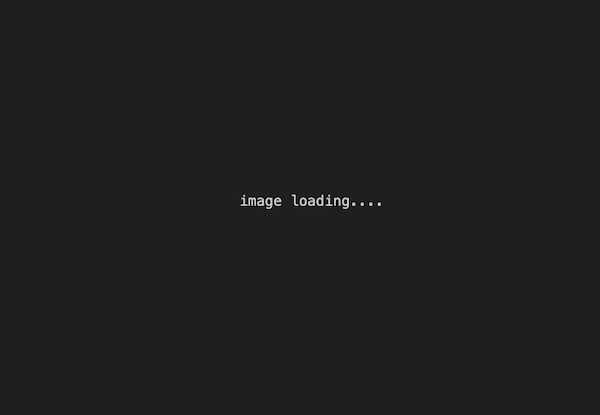
All the joints are simple rabbets. The lid is a single piece with rabbets sawed into all sides. These are done by making multiple parallel passes with the circular saw, with the blade set to the depth of the rabbet.
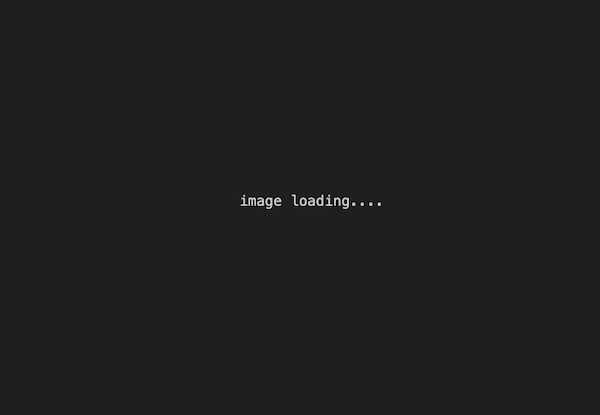
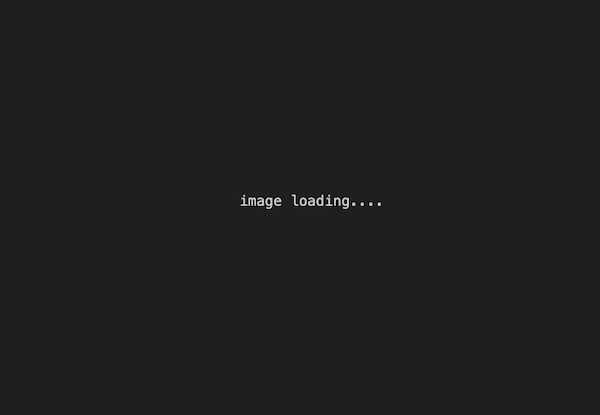
The box is finished with poly-crilic, a can of which my sister-in-law had given to me and which I had previously used to refinish a stool I found on the street. It doesn't look as nice as true polyurethane, but it's much easier to work with.
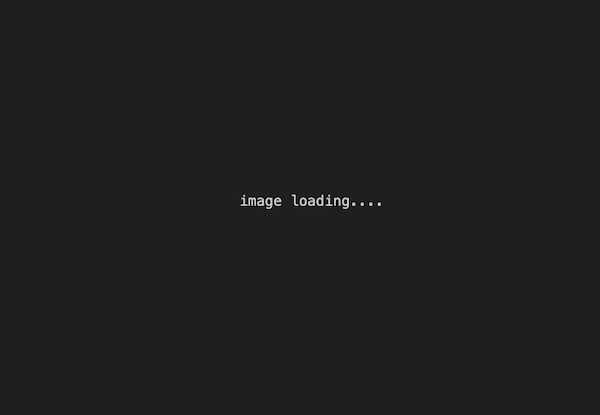
Desk drawers
One of the two desks in my bedroom is the Ikea "Micke" desk. I never liked the cabinet, which contains stationary shelves behind a door. Items at the back of the shelves are inaccessible and everything gets dusty.
I thought it might be fun to try to modify the desk. Because it's cheap, has been with me for seven years through three different apartments, and because I find it pretty ugly, I wasn't concerned about tearing it up a bit.
The drawer bottoms are all made from the original shelves or, in the case of the bottom drawer, a cut piece of what was once the cabinet door.
The rest of the drawer sides are from a plywood display case discarded by the smoke shop right next door to my apartment. It's kind of tacky stain; mixing that color with the black of the desk and the blonde wood of the drawer pulls makes for an odd aesthetic, but I like it.
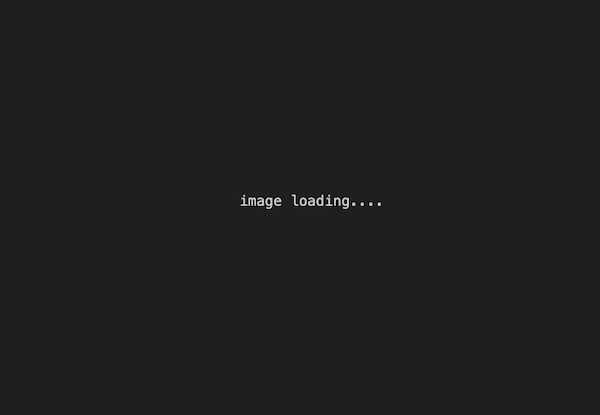
The drawer pulls were originally triangular pieces cut to reinforce one of the legs of the kitchen table, whose joints with the apron had unfortunately not closed well. However, the pieces weren't quite square enough to use for that purpose, so I drilled cylindrical holes through them with a hole saw bit, sanded them down, and super-glued them right onto the drawer fronts.
The drawer slides were decorated bits of edge banding that also came from the tobacco shop display case. I sanded and coated them with candle wax, which has made for surprisingly smooth operation.
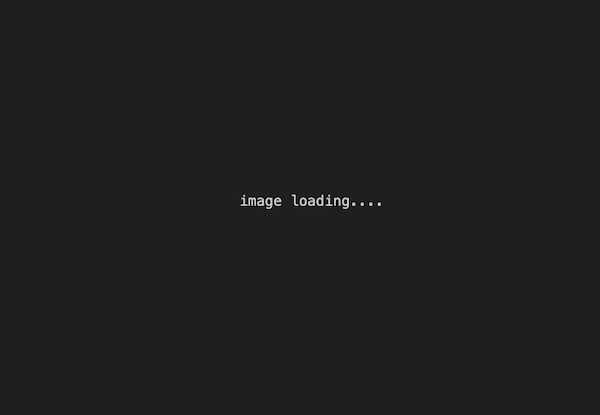
This was my quickest and laziest project. I joined everything with screws and used no glue at all. Still, everything seems strong and the drawers work well, which is all I hoped for.
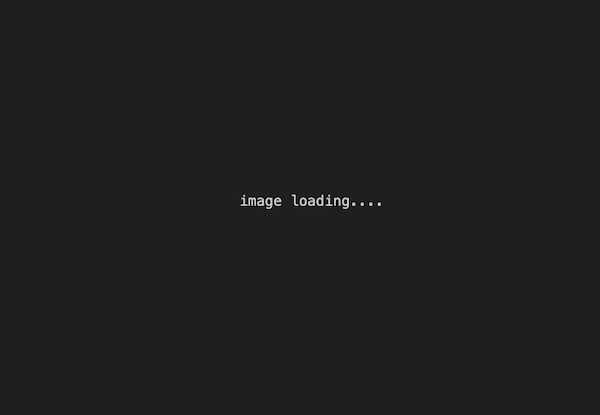
Stools
After my brother and sister-in-law moved into a new apartment, they needed new stools for their kitchen. I offered to build some to spec.
This was my most ambitious project, because the product wasn't for me, because I wanted to use mortise and tenon joinery, and because I had to make two of them.
There were a few material sources:
- Ikea shelves like the ones used for the bread box (the seats)
- A discarded softwood bed frame (four legs and foot rests)
- Leftover from the boards used for the kitchen tabletop (two legs)
- Leftover from the butcher block used for the kitchen table apron/legs (two legs)
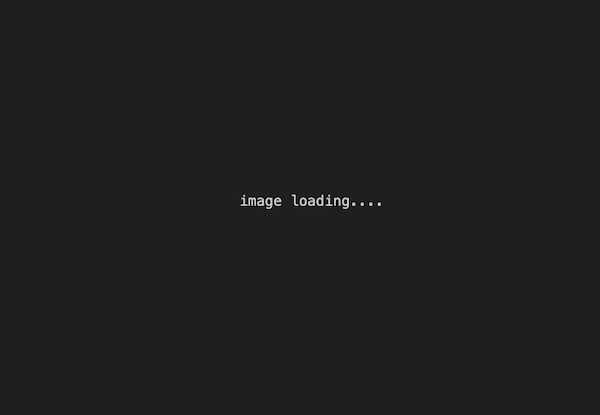
Circular saw tenons
Cutting tenons with a circular saw is ambitious and not necessarily advisable.
It's not too difficult to cut rabbets with a circular saw by making multiple parallel cuts, starting at the inner edge of the rabbet and moving outward, with the blade depth set to the desired depth of the rabbet. In principle, a tenon can be cut the same way, but on all four faces instead of only one.
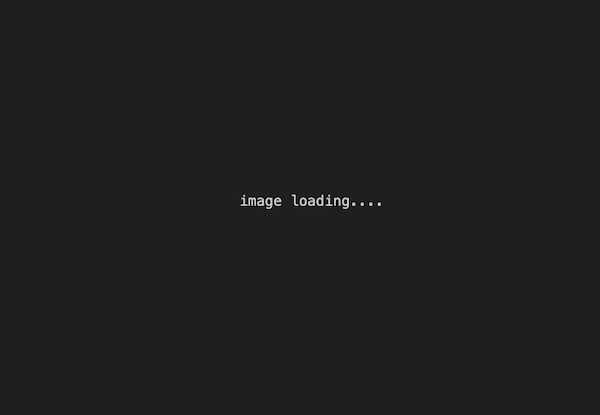
One of the challenges is getting the inner edge (shoulder) of the tenon to match perfectly on each of the four edges. Failing to do so will lead to gaps when the joint is closed. My shoulders were a complete mess, and though the joints closed tightly, there are conspicuous gaps.
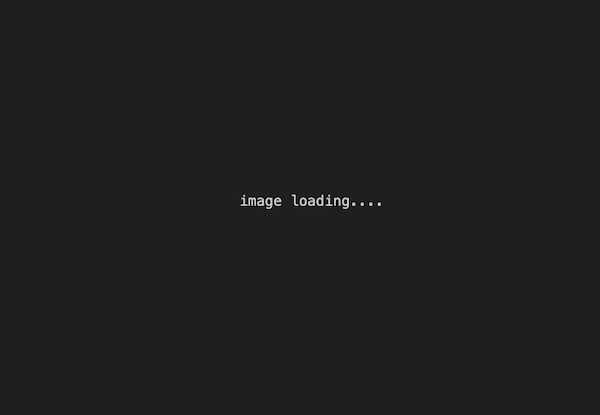
Hand drill mortises
Making mortises with hand drill is much easier than cutting tenons, but I doubt I could have done it without a self-centering doweling jig. (I have one, unfortunately not cheap but very handy, from "Dowl-it").
A hole is drilled at each end of desired mortise location, centered at one radius distance from the edge of the mortise. It's then fairly trivial to drill a series of holes between the two ends that results in a rounded rectangle.
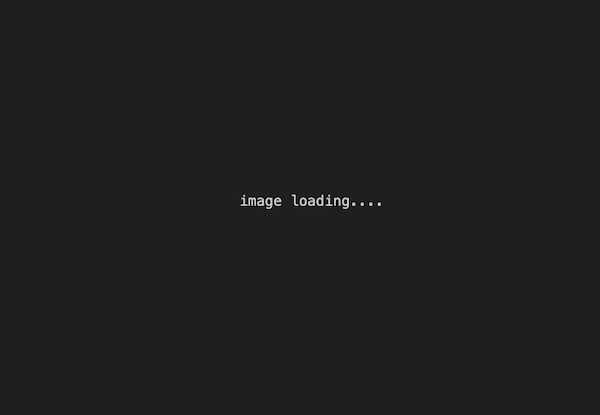
I was pleased to find that, in spite of the sloppiness of my tenons, all parts fit together very nicely.
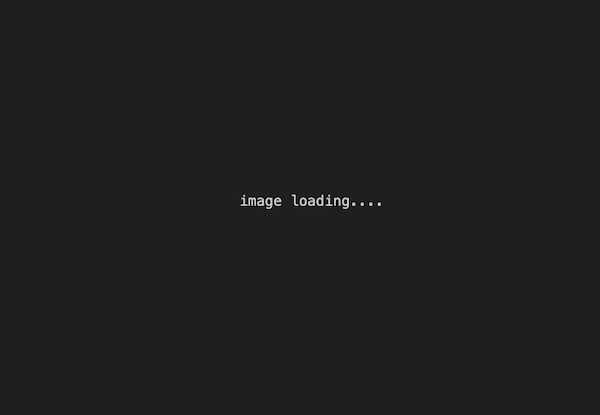
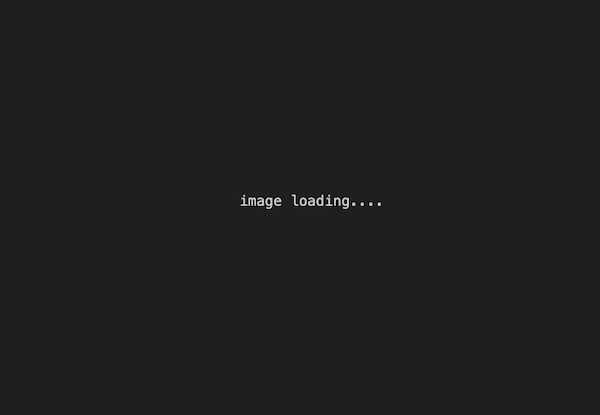
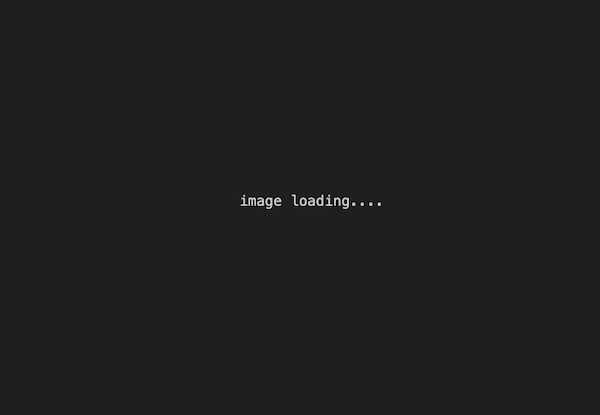
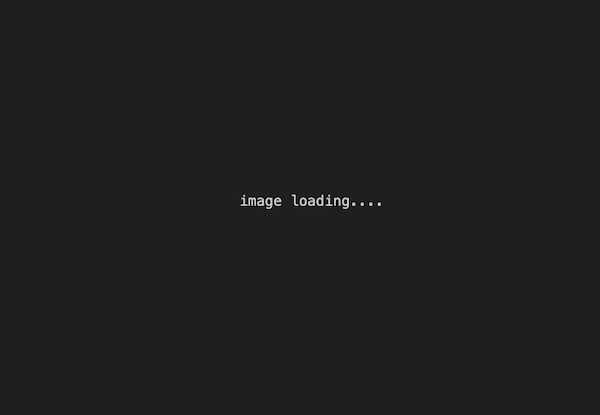
One special aspect of the specification for these stools was the footrest height, which was set slightly higher than usual. This was requested to create a flat lap. My brother and sister-in-law's cat, Sparrow, likes to lie on the laps of people sitting on stools, and she demands a flat lap.
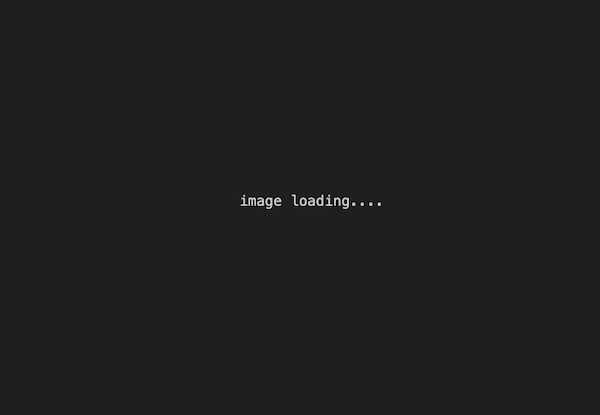